Our Dockweiler process vessels ensure safe and efficient handling of organometallic compounds – from storage to disposal. They are manufactured to the highest standards, with optimized geometries and durable materials for a long service life. Precise orbital welds, electropolished surfaces and high-quality materials enable optimal use of media, complete emptying and easy cleaning. Whether for solids or liquids – Dockweiler offers customized solutions for the most demanding requirements.
Process Vessels
Dockweiler process vessels are known for their high quality and precision. From the careful selection of materials to the perfect electropolished surface, our bubblers ensure maximum efficiency, complete emptying, easy cleaning and maximum process reliability when handling high purity media. Perfect for demanding production processes in the semiconductor and fine chemical industry.
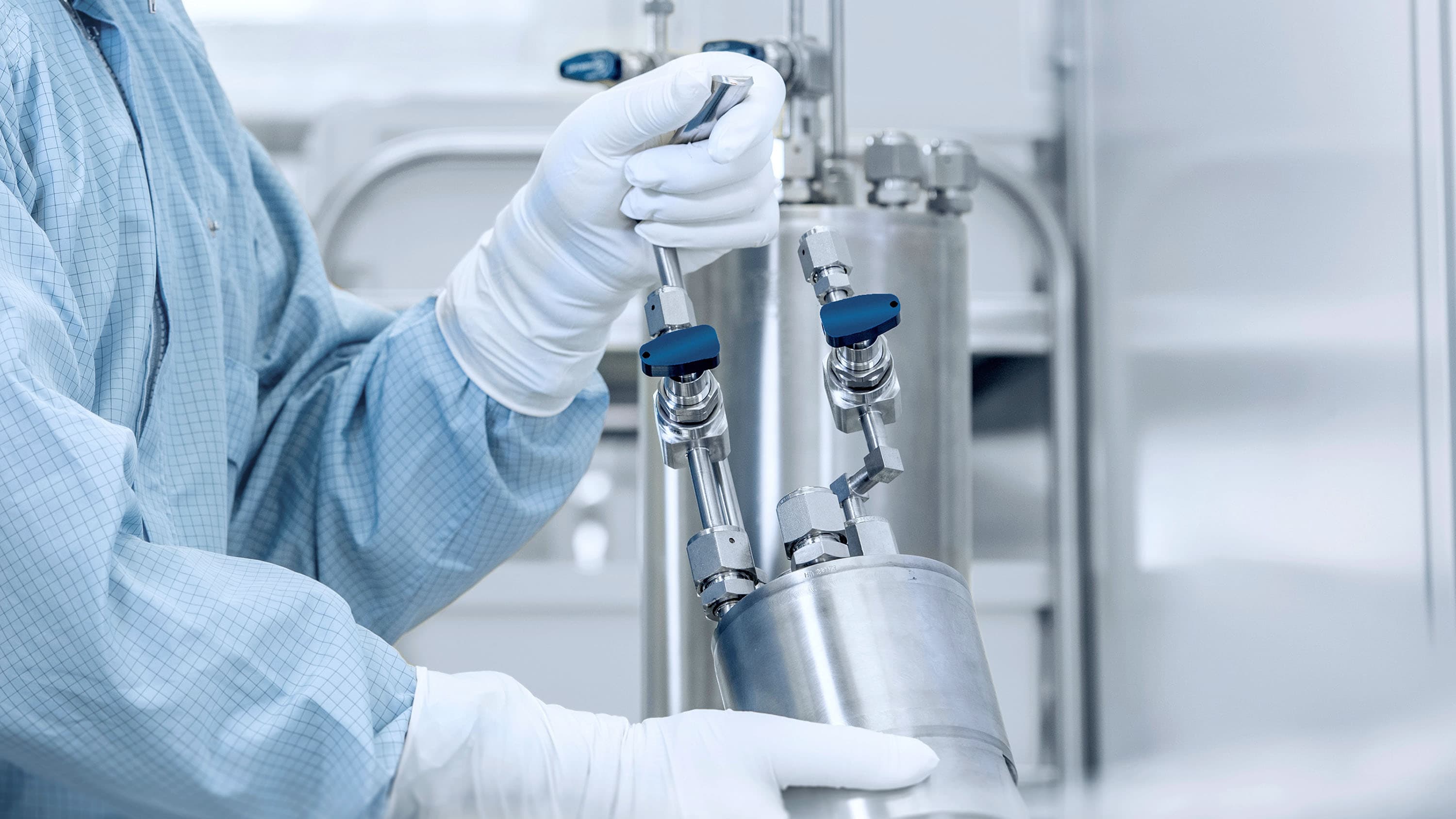
Safe storage and transportation of organometallic compounds – with Dockweiler bubblers
Bubbler Design
1 Inlet valve
2 Outlet valve
3 Crossover function (optional)
4 Inspection Port
5 Dip tube (inlet)
6 Vapor space tube (sampling tube)
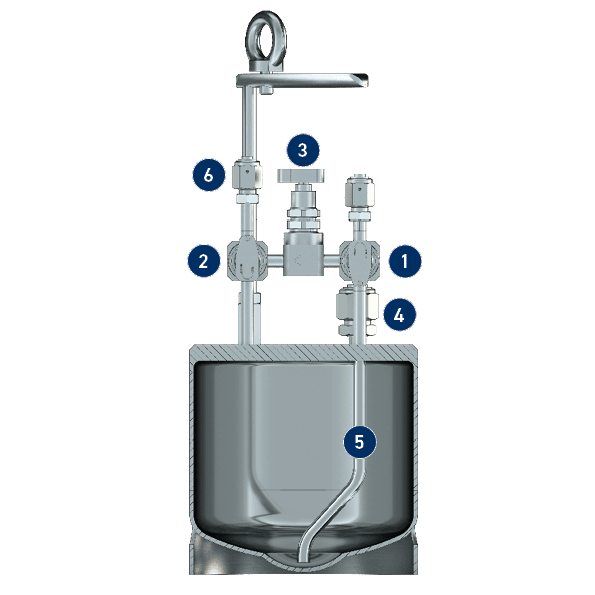
Overview
Our bubblers are made from the following materials as standard. We also offer optional versions in special materials:
- 1.4404
- 1.4435
- S31603 (316L)
Special materials:
- UNS N08367 (AL-6XN)
- UNS N08904 (904L)
- UNS N06022 (C22)
Dockweiler bubblers are available in the following dimensions and volumes:
- Volume: 200 ml to 56 l
- Diameter: 63.50 mm to 273.00 mm
- Cylinder height: 82.00 mm to 1,070.00 mm
There is a wide range of connection and equipment options for our bubblers. This allows you to configure them according to your specific requirements.
- Different valve options
- ZeroCon connections
- Level sensor
- Additional connection
- DOT and ADR on request
- Temperature control unit
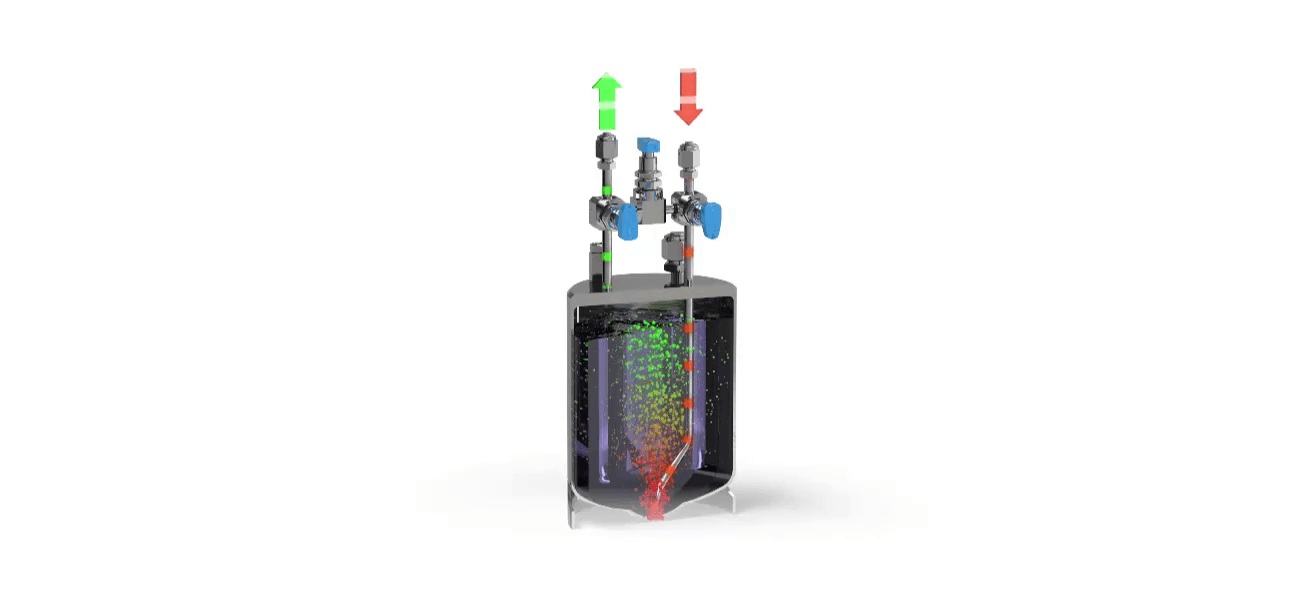
Process vessels for your demanding applications
Let us find the best solution for your process requirements together – talk to our experts about the customized container systems from Dockweiler!
All benefits at a glance
No dead spaces
Thanks to the orbital welding process, there are practically no dead spaces. This minimizes deposits and improves media flow.
Maximum output
Thanks to the optimized geometry, more than 99 % of the organometallic compound is used. This ensures maximum efficiency in the process.
Temperature stable
The containers can withstand temperatures from -50°C to +100°C. This makes them ideal for a wide range of processes.
Optimized dip tube geometry
Developed together with the industry: The optimized geometry ensures maximum saturation and throughput in the process.
No material outgassing
All wetted components are made of stainless steel 1.4404/316L or special materials. This ensures maximum purity.
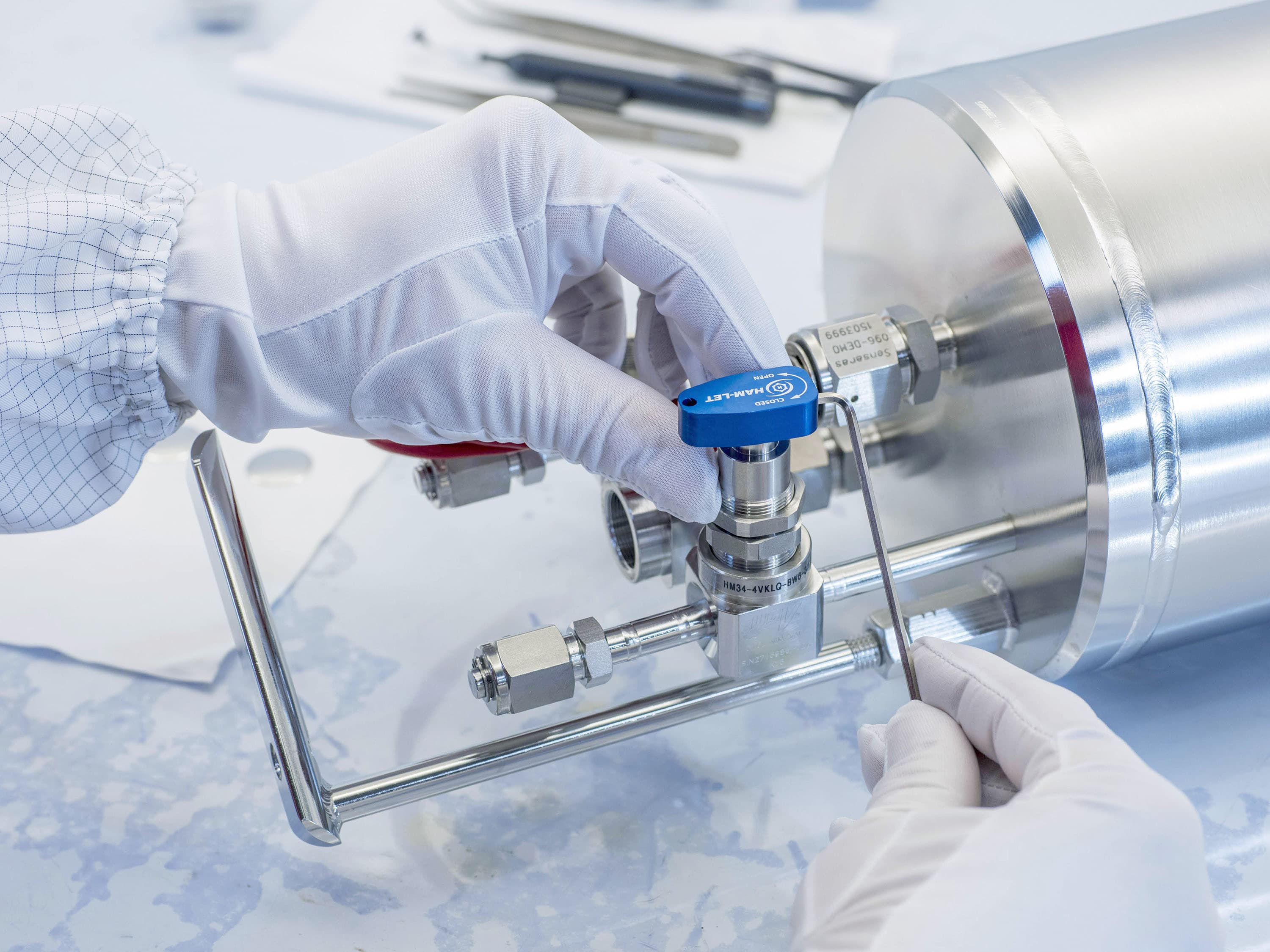
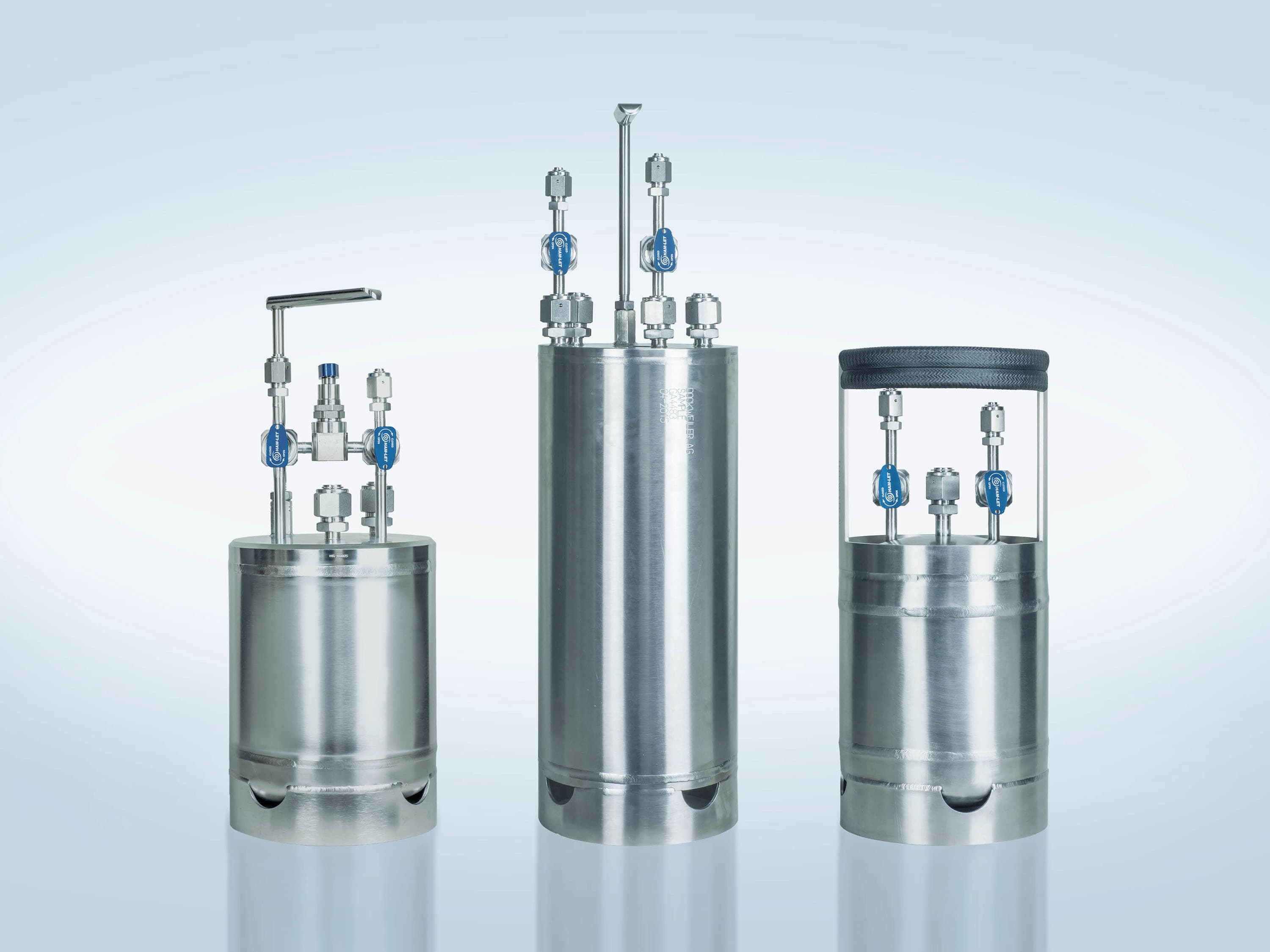
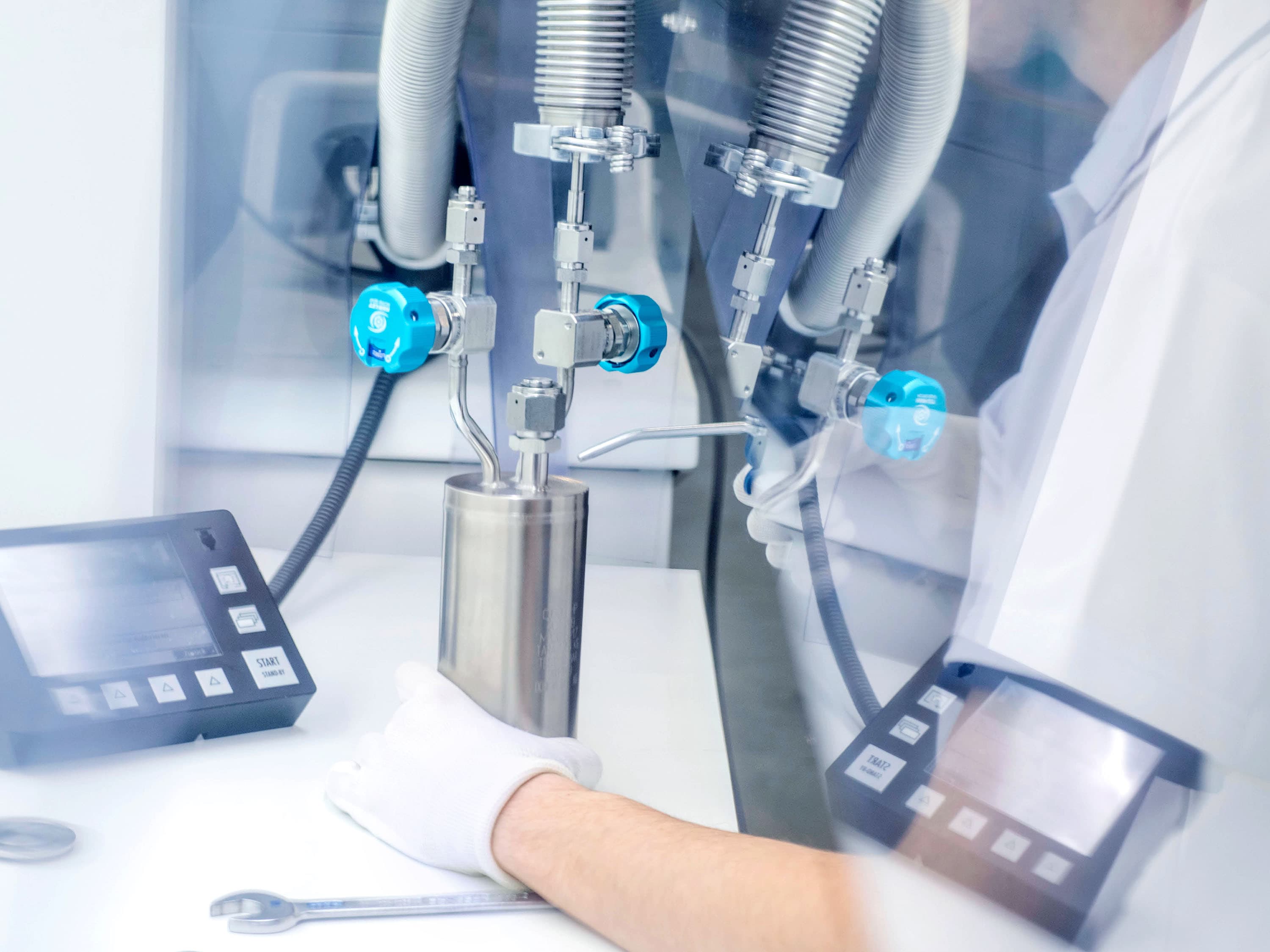
More information
Advice that goes further
From material selection to specific applications - our team supports you with precise, application-oriented advice. Find out how we can improve your processes. Find out more!
Clean processes
With Dockweiler's specialized cleaning methods, we guarantee not only the absence of residues, but also the perfect surface quality of your components. Reduce risks and increase your efficiency. Discover now!
A matter of cleanliness
Where cleanliness counts, we are at home: with state-of-the-art technology and many years of experience, we produce ultra-clean systems for your most sensitive applications in the cleanroom. Find out more about our cleanroom solutions!