Welding is one of Dockweiler's core manufacturing competencies. In addition to our own welding processes, we have redefined the standard: at Dockweiler, we set the highest requirements of the current international standards (DIN EN ISO 5817/B, ASME BPE and SEMI) as our standard. With over 40 years of experience, Dockweiler is a pioneer in the field of orbital welding technology. We at Dockweiler continuously develop the efficiency and quality of our processes using modern technologies.
High-quality welds for maximum process reliability
The safe transportation of high-purity gases and liquids places high demands on the quality of stainless steel tube systems. This applies in particular to their weld seams in terms of tightness and corrosion resistance.
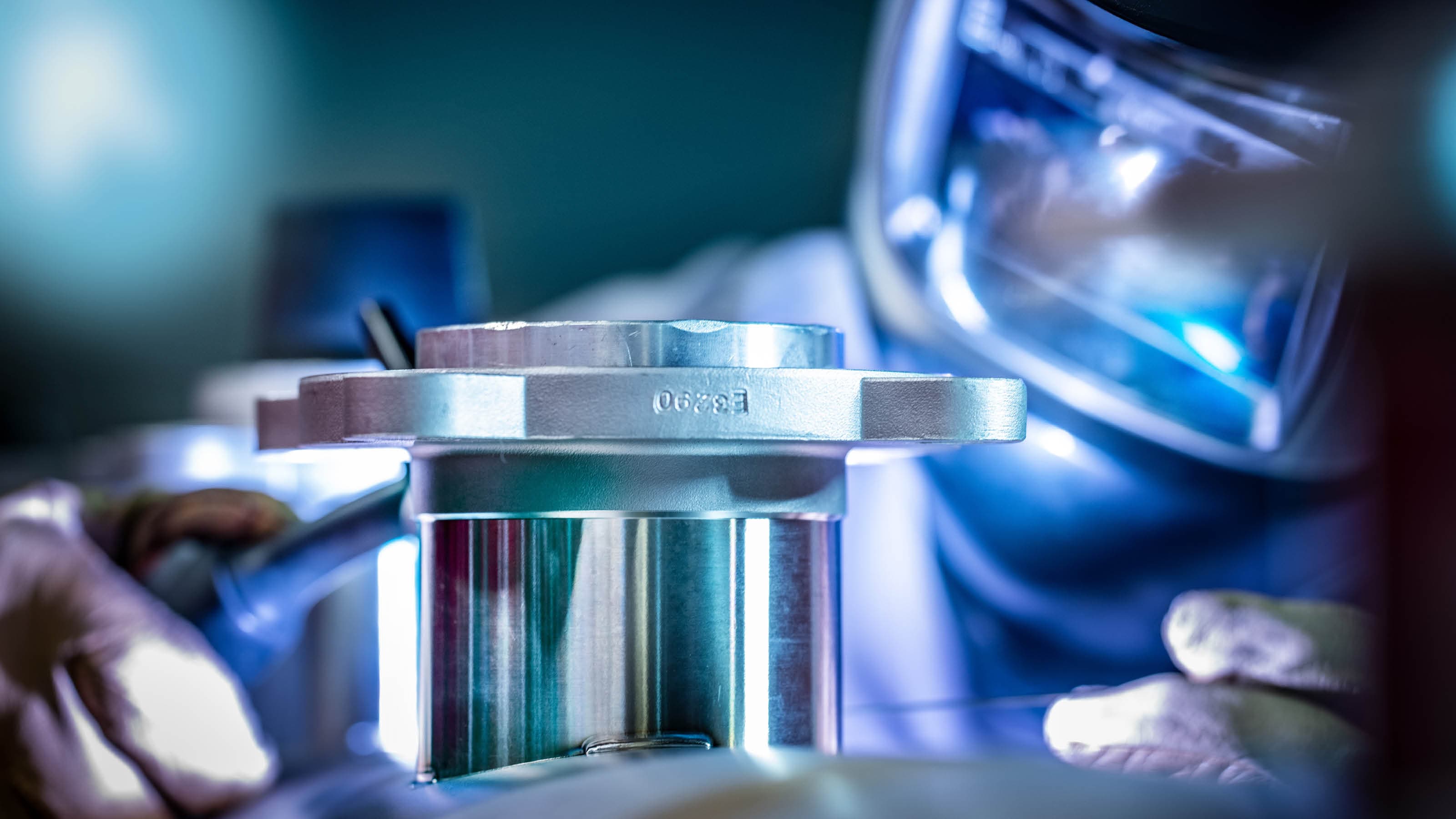
Experience is the key
With a special process known as inside orbital welding (IO), Dockweiler is opening up new possibilities for innovative manufacturing concepts. In this process, the welding torch used in mechanized TIG welding is guided along the inside diameter of a tube. This technology has proven particularly effective for thin-walled tubes and demanding applications where high weld quality and cleanliness are required. Internal orbital welding enables precise control of the welding process and reduces welding distortion. The automated process control enables us at Dockweiler to achieve a high level of precision and repeatability with every weld.
The processing of stainless steel tubes for demanding applications requires strict compliance with all relevant standards (e.g. ISO 15614) - from welding technology to complete documentation, testing and certification of the weld seams. Dockweiler carries out a complete seam inspection after every welding process. Continuous pressure and residual oxygen monitoring and the use of shielding gases such as argon or helium ensure controlled conditions and prevent oxidation and contamination. The δ-ferrite content is reduced to ensure quality. All parameters are recorded digitally and traceably.
At Dockweiler, high-purity components such as manifolds for inert gases or comparable demanding applications are manufactured under controlled cleanroom conditions (ISO class 4). This means welding in a high-purity working environment with controlled air particle concentration. The welding processes must not cause any particle entry. Contamination of the weld or the product must also be avoided. The level of welding in a class 4 clean room is comparable to that in highly regulated industries such as the semiconductor industry, the pharmaceutical industry, medical technology, the aerospace industry and the optical industry.
Our customers know that a high level of cleanliness and surface quality is essential for perfect weld seams.
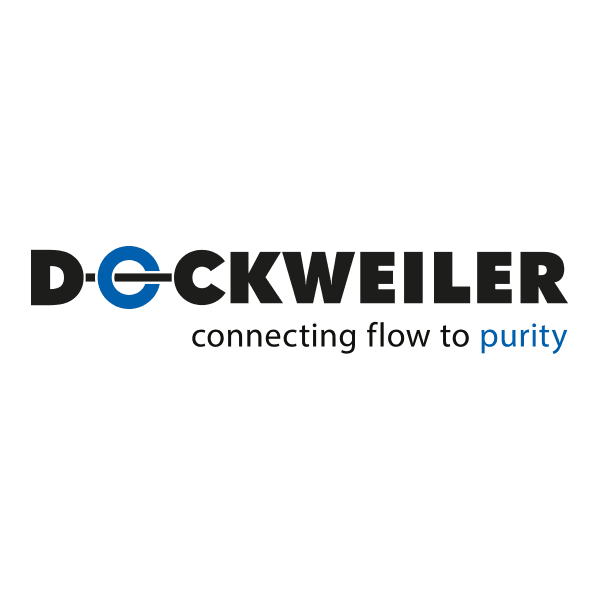
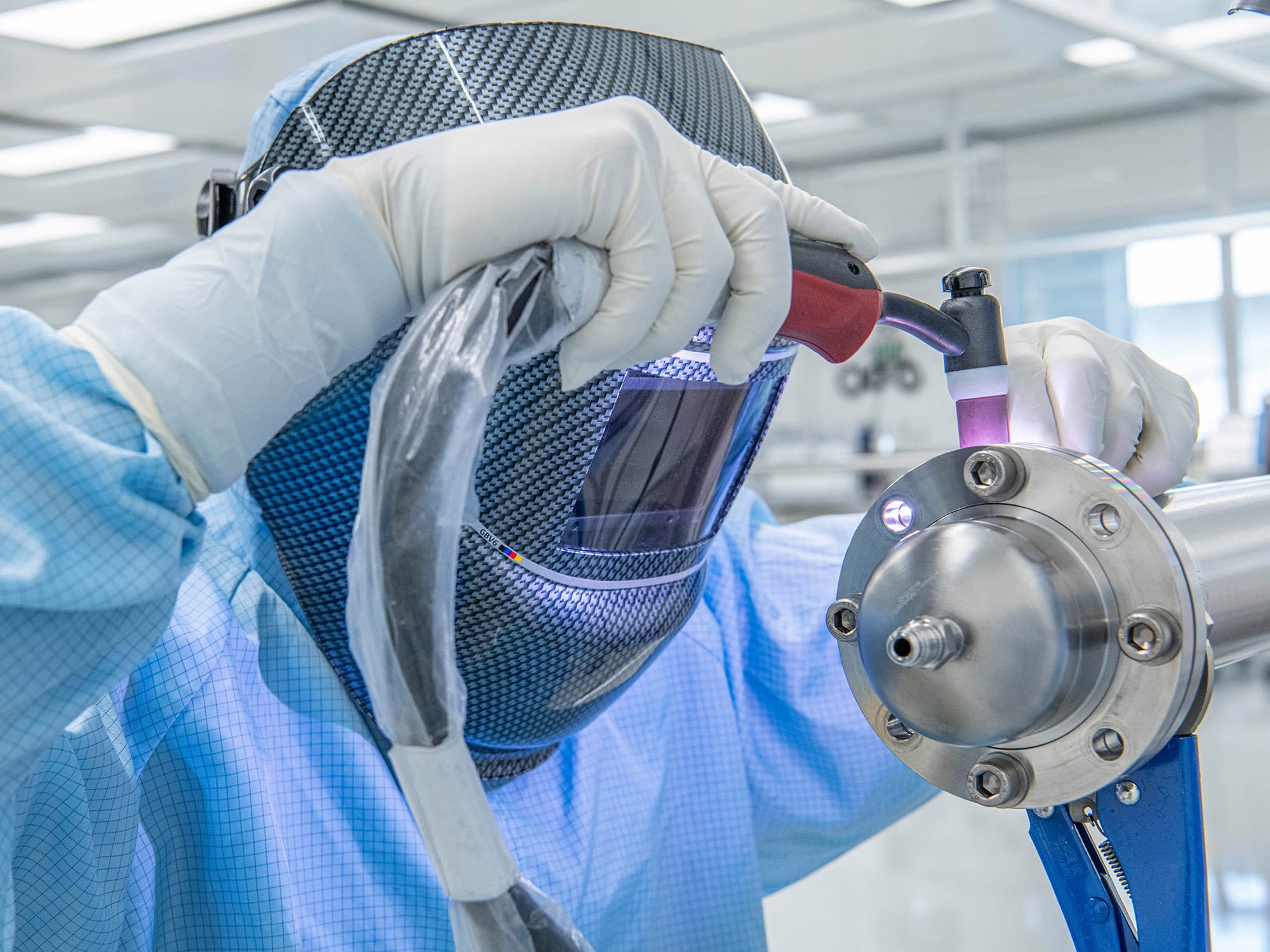
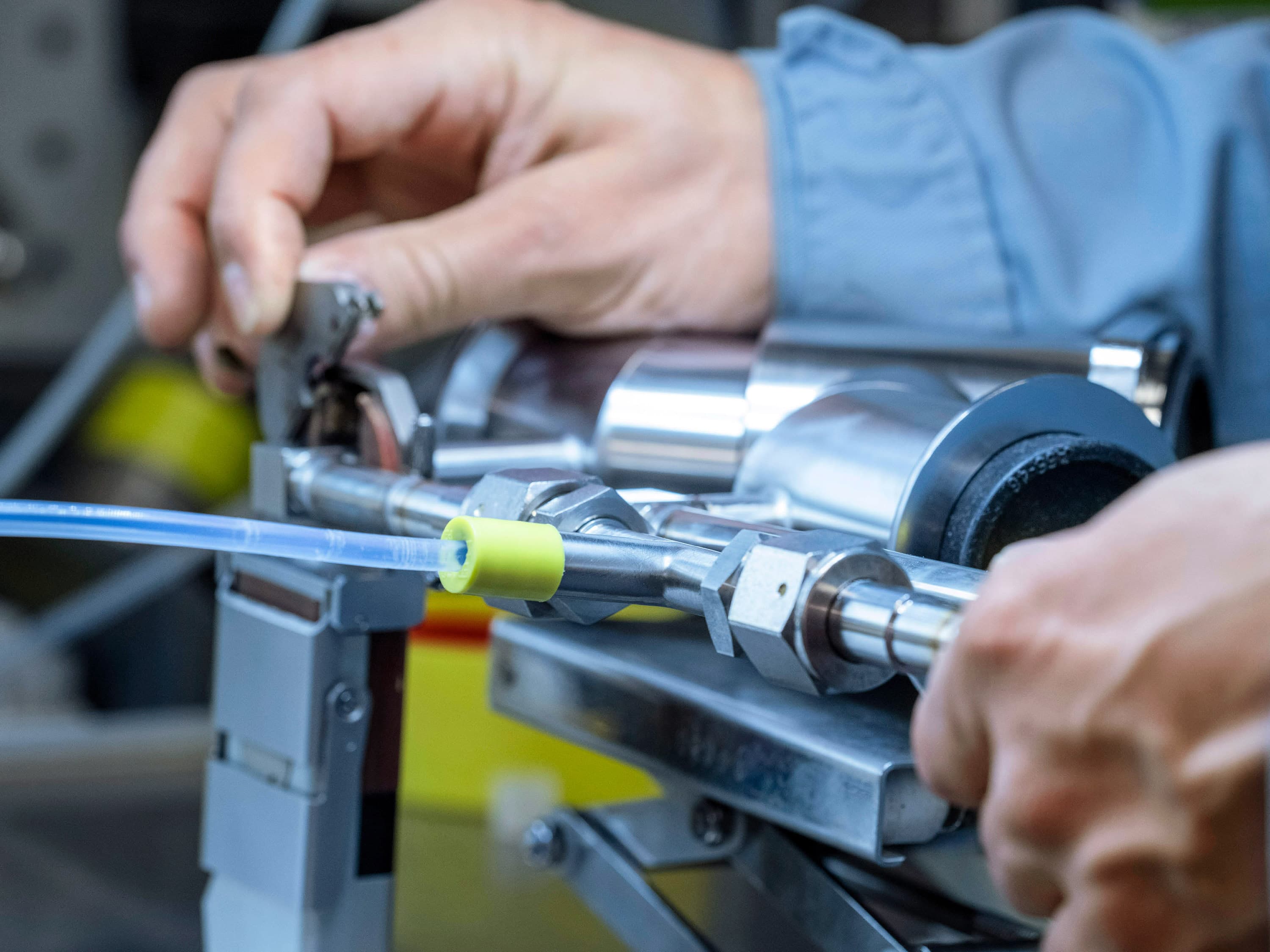
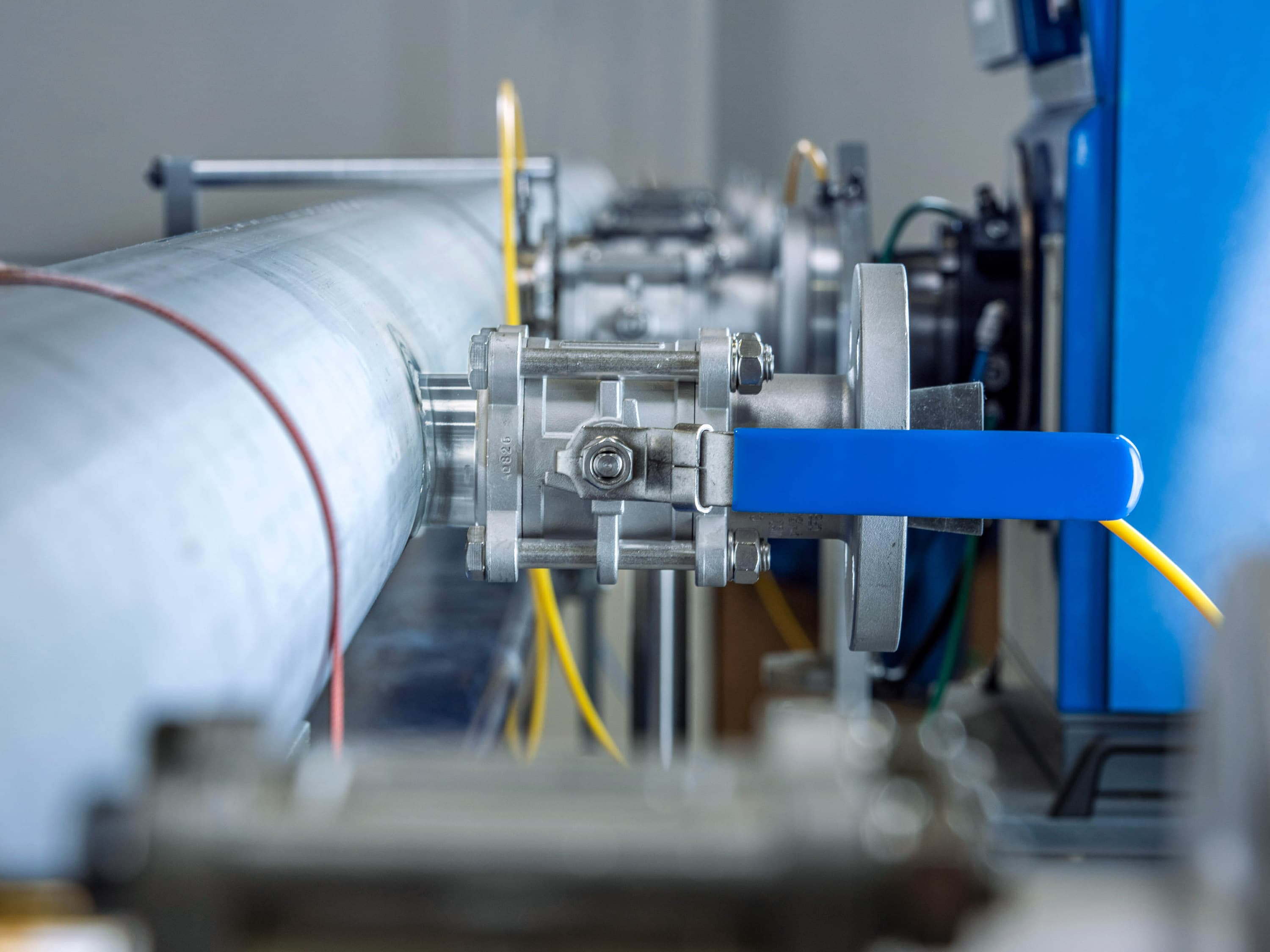
Our Expertise - Your Benefits
Decades of welding expertise
With over 40 years of experience and around 5,000 welds per week, Dockweiler is the technology leader in orbital welding. International standards are not our goal - they are our standard.
Reproducible top quality
With state-of-the-art orbital welding technology, we achieve exact repeatability - even with complex geometries. Automated processes and precise control minimize distortion and ensure consistently high quality.
Documented safety
Every weld seam is produced under strictly monitored conditions and 100% tested. All parameters are digitally recorded and traceable - for maximum transparency and standard-compliant quality assurance.
Maximum process reliability
High-purity gases and liquids require absolute tightness and corrosion resistance - especially at the weld seams. Dockweiler ensures reliable quality along the entire process chain with precise processes and complete testing.
Purity at the highest level
In our clean room production (ISO class 4), we produce high-purity components for strictly regulated industries such as semiconductors and pharmaceuticals. This reliably prevents any form of particle entry or contamination.
More information
Optimized process vessels
Dockweiler process vessels guarantee precise handling and maximum efficiency for your demanding production processes. Benefit from optimized geometry and robust material selection. Click here to find out more about our solutions!
Advice that goes further
From material selection to specific applications - our team supports you with precise, application-oriented advice. Find out how we can improve your processes. Find out more!
Quality without compromise
The highest quality in every detail - that is our claim. We guarantee that all our products, from the raw material to the finished product, meet the highest standards. Our quality assurance ensures complete traceability and gives our customers peace of mind at every stage of the process. Click here to find out more.