For safe manufacturing processes, we offer specific inner surfaces from bright finished to electropolished. With our decades of experience in mechanical and electrochemical surface treatment and finishing, we offer the optimal quality for your applications. The continuous development of surface qualities is the result of innovative manufacturing processes and special solutions for customers. Our work in international professional organizations such as SEMI, EHEDG, AiF, GfKORR and VDMA, as well as our participation in standardization work in ASME, ECISS and DIN, provides further impetus. Regular audits document the high quality of our products.
Surface Treatment
In highly technical industries – for example in the semiconductor and pharmaceutical industries – the highest standards of purity and precision are essential. The surface treatment of stainless steel tubes and fittings has a significant role to play in meeting the requirements for purity and resistance in highly sensitive production processes. This is Dockweiler's specialty.
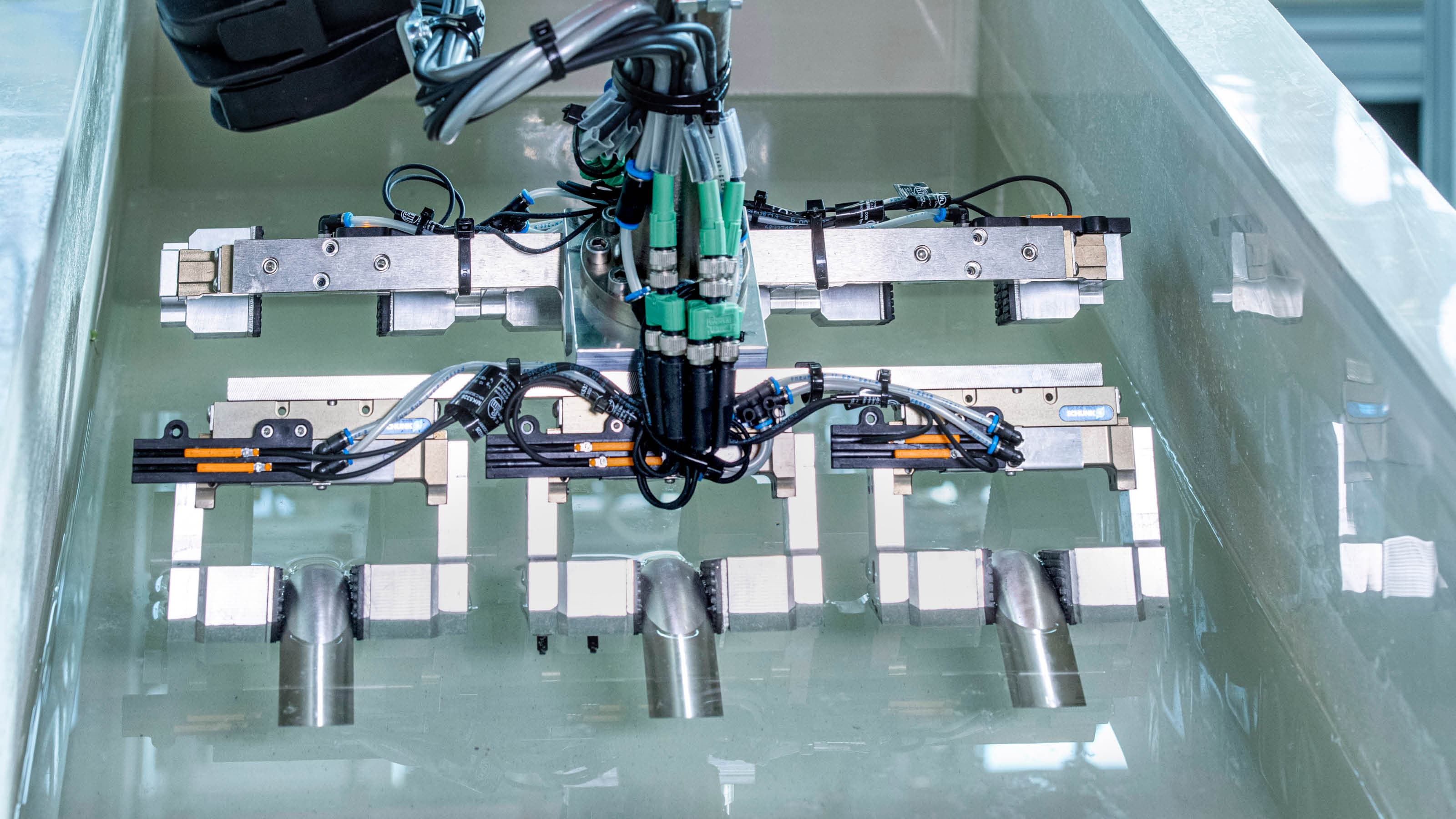
Inner surfaces that are second to none
Surfaces in detail
Here microscope images (300:1) show our different surfaces - because often things are in detail.
In electrochemical processes, material removal is specific. In the anodic process, the material is cleaned with an abrasion of 3 to 5 µm. In the electropolishing process, the material removal is significantly higher. It is up to 20 µm. This results in a particularly smooth and shiny surface - up to a quality of Raavg. ≤ 0.13 µm.
The surface treatment of complex special components requires a high degree of precision and expertise. In addition to standard fittings and tubes, we also finish complex special components such as manifolds, CIP lances and vessels. Our specialized processes ensure that even highly complex geometries, tight tolerances and the special requirements for purity and corrosion resistance are reliably met. Dockweiler offers individual solutions that take into account both functional and economic requirements.
At Dockweiler, we see sustainability as an integral part of our production processes. This also applies to the surface treatment of stainless steel tubes and fittings, where we always use environmentally friendly processes and resource-saving technologies. With innovative processes, we reduce the use of chemicals and minimize energy consumption without compromising on quality and the highest purity requirements.
When it comes to surface treatment, we not only ensure the highest quality, but also sustainability by using resources efficiently.
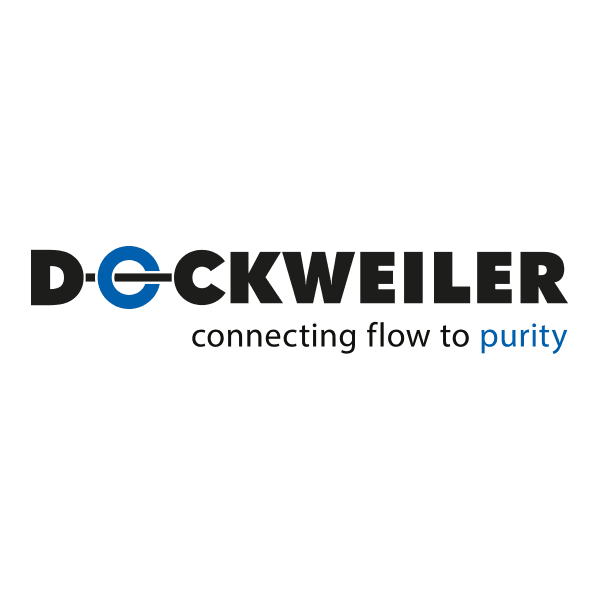
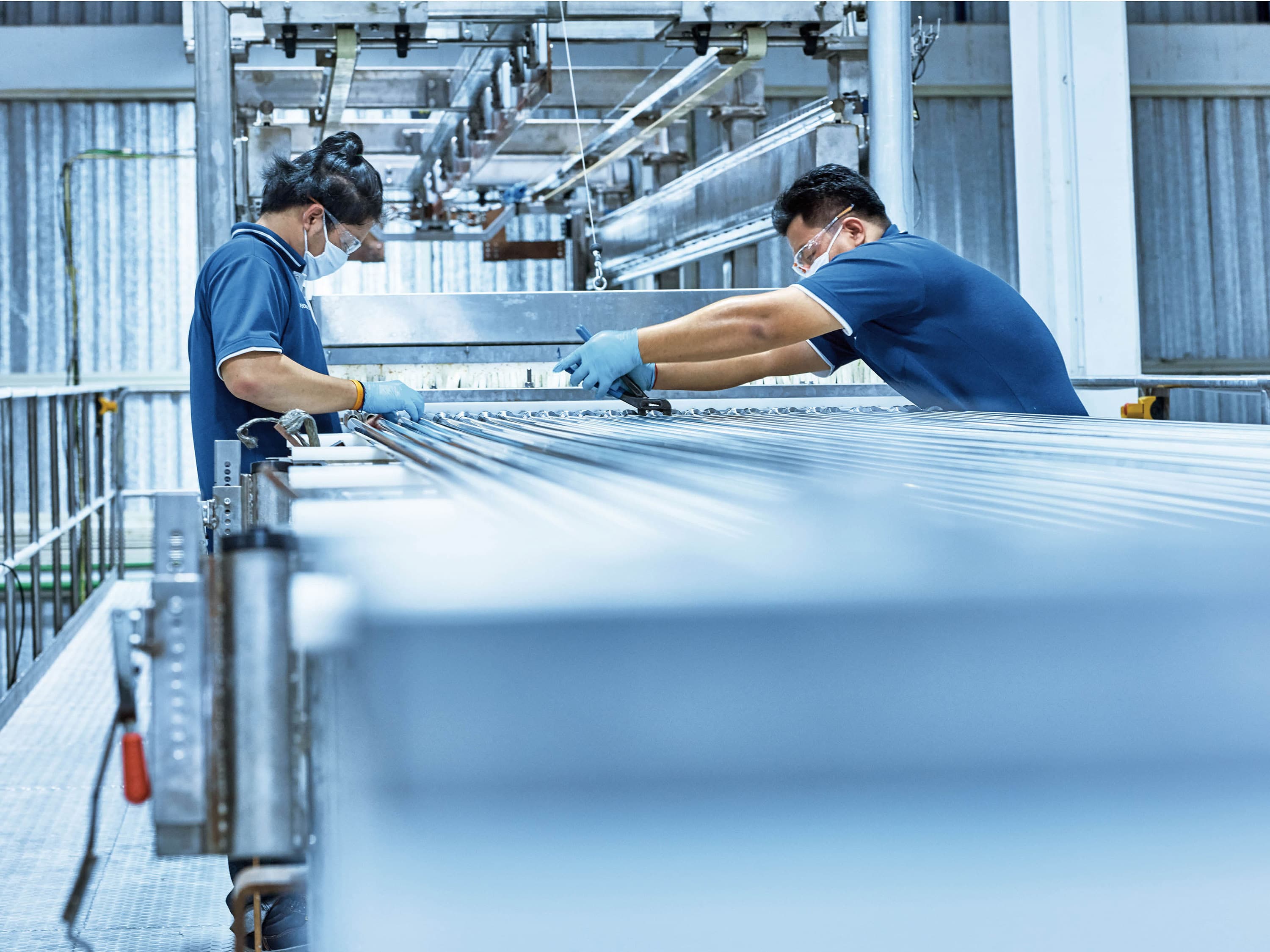
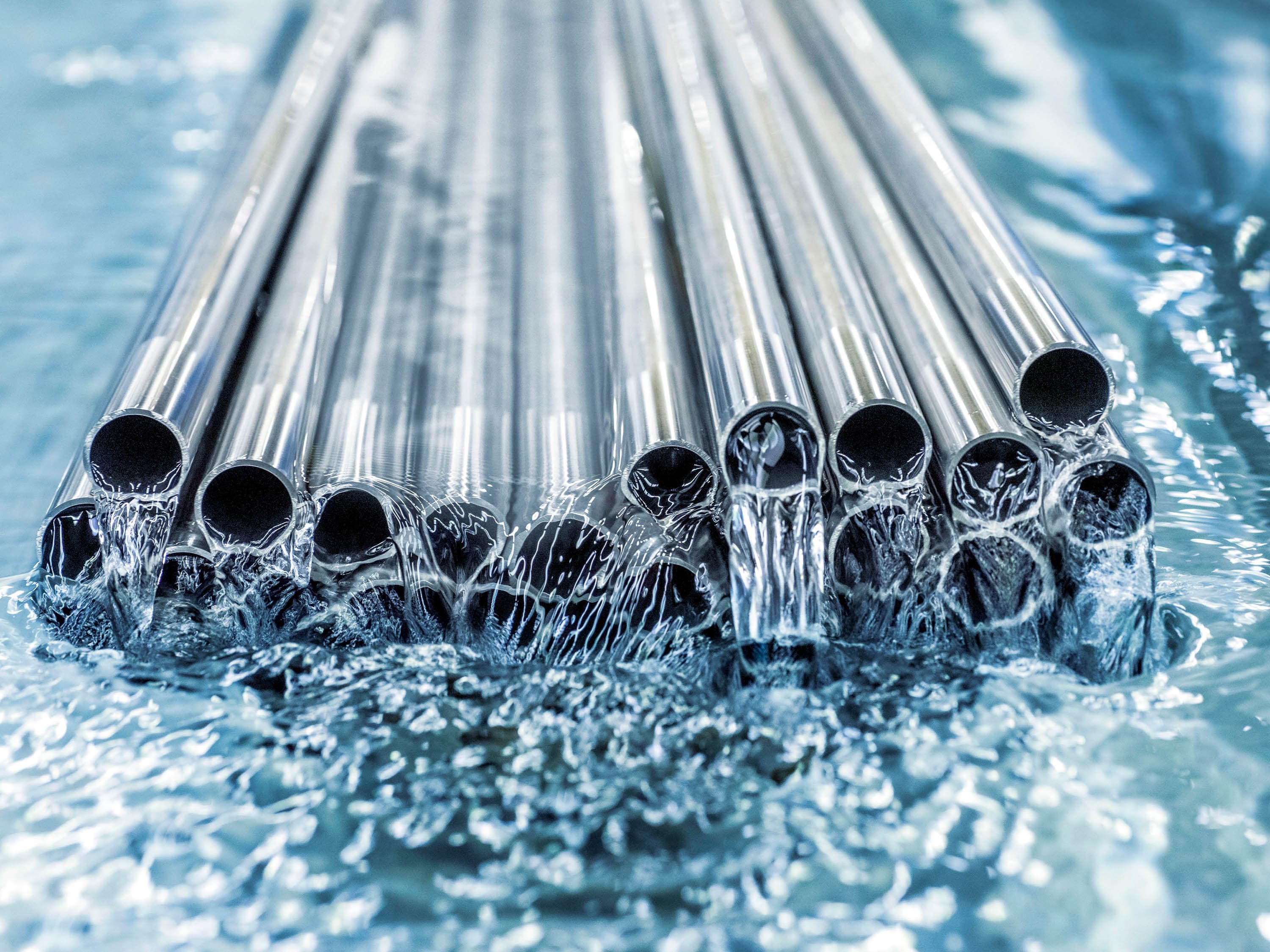
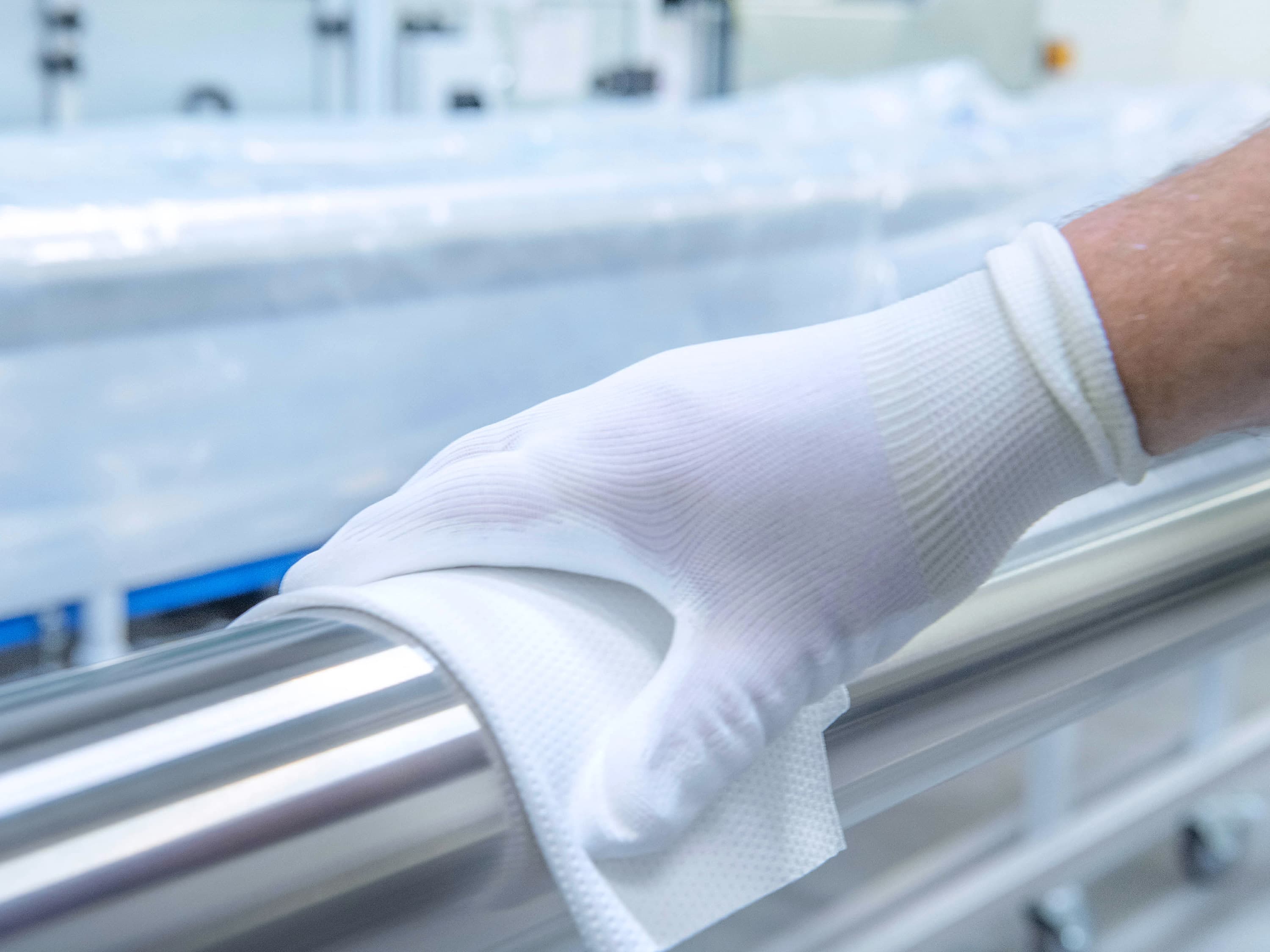
Do you need the highest surface quality for your manufacturing processes?
Dockweiler offers customized surface treatments that meet the highest standards – from mechanical processes such as grinding and polishing to electropolished surfaces.
Customer Benefits
Customized solutions
Dockweiler offers customized surface solutions for complex parts and standard components.
Optimized hygienic design
The specially finished surfaces minimize deposits and make cleaning easier, effectively preventing contamination.
Certified quality
All machining processes meet international standards and ensure the highest safety and quality standards.
More information
Flexibility without compromise
Maximum flexibility and the highest purity - with electropolished stainless steel corrugated hoses from Dockweiler Flextron, you can guarantee uncompromising quality for your processes. Ideal for applications in microelectronics and fine chemicals.
Optimized process vessels
Dockweiler process vessels guarantee precise handling and maximum efficiency for your demanding production processes. Benefit from optimized geometry and robust material selection. Click here to find out more about our solutions!
Quality without compromise
The highest quality in every detail - that is our claim. We guarantee that all our products, from the raw material to the finished product, meet the highest standards. Our quality assurance ensures complete traceability and gives our customers peace of mind at every stage of the process. Click here to find out more.